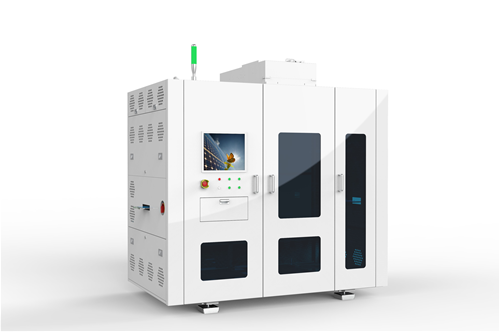
DR Laser has acquired the patent of Israel-based research centre, Utilight, to create the world’s first - Pattern Transfer Printing (PTP™) system.
This equipment is created to precisely deposit microscopic silver lines onto solar cells, in a process known as “metallization”.
The PTP™ works by filling silver paste into a patented-design, trench-shaped, organic polymer carrier tape. The process is followed by the alignment and scanning of a high-power laser beam upon the trenches, which completes the material transfer of silver paste from the carrier tape onto the surface of battery cell.
Our method has achieved an all-around improvement in the transfer printing of metal gridlines for battery cells. In comparison with conventional methods, the PTP™ technology is a contactless process which enables narrower linewidths and better aspect ratios, enhancing the efficiency of the solar cell, reducing slurry consumption, and lowering the production cost of the battery cell.
In today’s industry, metallization line integration, and as a standalone equipment.